Lean Manufacturing
Lean reduces costs, improves quality and speeds up delivery by eliminating activities with no added value in a process by identifying and eliminating waste.
What is Lean Manufacturing?
- Lean Manufacturing – is a way to eliminate waste and improve efficiency in a manufacturing environment.
- Lean focuses on flow, the value stream and eliminating muda, the Japanese word for waste.
- Lean manufacturing is the production of goods using less of everything compared to traditional mass production: less waste, human effort, manufacturing space, investment in tools, inventory, and engineering time to develop a new product.
- Lean reduces costs, improves quality and speeds up delivery by eliminating activities with no added value in a process by identifying and eliminating waste.
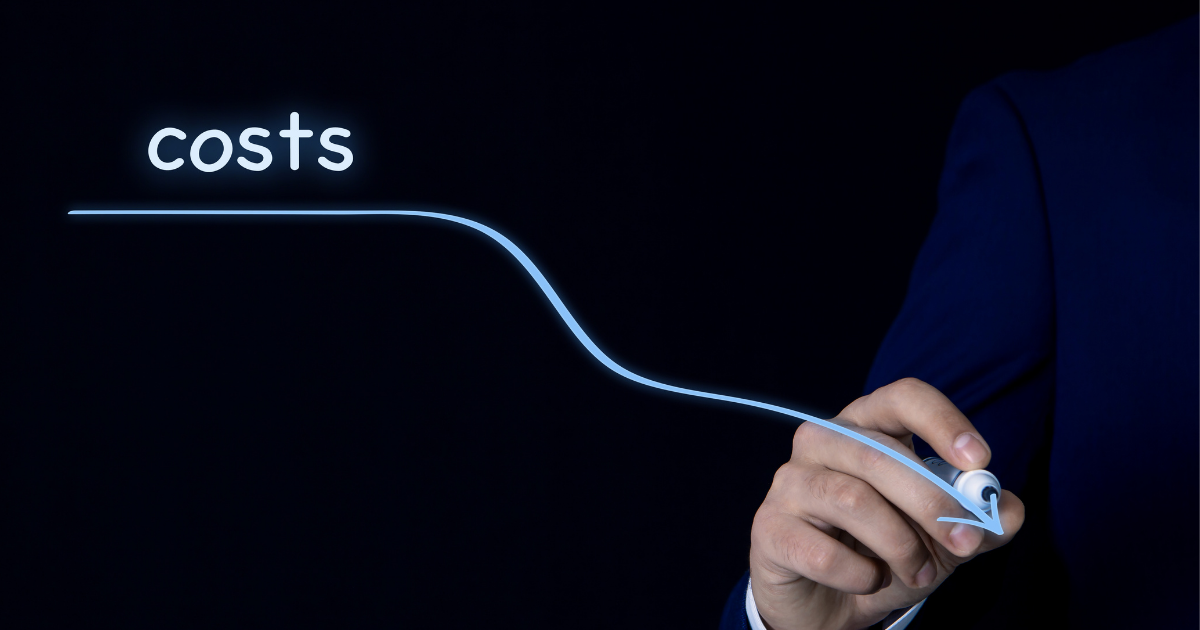
Lean Manufacturing Course Objectives
• evaluating and quantifying opportunities for improvement;
• improving efficiency, reducing inventory and reducing operating costs;
• ROI analysis - Increasing profitability;
• Lean project management using DMAIC methodology;
• integrate Lean with your corporate strategy using Lean vision.
Who should attend Lean Manufacturing Course?
The course Lean Manufacturing is addressed to staff working in industry. This seminar is especially useful for individuals who are Responsible for improving processes by analyzing , selecting and implementing permanent solutions, People participating in process improvement analyzes and want to identify and find optimal process conditions, Process Design engineers, Quality engineers, Process engineers that are assigned responsibility for leading quality and productivity improvement.
What you will learn?
- Lean principles in the organization - Defining the principles and their implementation
- Lean concepts and tools -Defining and describing concepts such as value chain, analysis and optimization of manufacturing flow and tools commonly used to eliminate losses: 5S, Problem Solving, VSM - Identification and Analysis of Activities with added value and without added value, Visual Factory, Total Productive Maintenance
- current Lean Practices
- changes in Lean, new concept of Industry 4.0
Day 1
- Introduction
- Team Responsibilities – RACI matrix
- DMAIC
- Gantt Chart
- Process Flow Diagram - Process mapping
- SIPOC
- VOC - Data collection plans
- Project Charter
Day 2
- Lean Tools
- Waste analysis & Waste elimination Tools
- Pull Systems
- 5S
- Visual Factory
- Cycle Time Reduction
- Work Flow Analisys – SIPOC
- Value Stream –VSM
- Process Capacity
- Quick Changeover/Setup Reduction
Day 3
- Kaizen
- Lean Tools for Process Control
- Total Productive Maintenance
- Visual Management
- Visual Workplace
- Changes in Lean
- Current Lean Practices
- Case Studies